Digitalisierung und Innovation
Einer der wesentlichen Treiber unserer Strategie ist der Fokus auf Innovation, Digitalisierung und Automatisierung. Wir investieren massiv in den digitalen Wandel. Daraus ergeben sich, unterstützt durch strategische Partnerschaften, neue Produkte und Lösungen. Wir nutzen Daten, Vernetzung, KI und vorausschauende Instandhaltung, um den ständig zunehmenden Anforderungen unserer Kunden in einer digitalen Welt Rechnung zu tragen. Durch die Einführung von digitalen Lösungen können sich unsere Kunden jederzeit und von überall mit RHI Magnesita SpezialistInnen in Verbindung setzen und Probleme standortunabhängig lösen.
Fußabdruck der Werke
Wir optimieren den ökologischen Fußabdruck unserer Werke, um Herstellkosten zu reduzieren und den Fokus auf eine regionalere und flexiblere Produktion zu legen. Ergänzt wird dies durch ein Spezialisierungs- und Kostensenkungsprogramm, das Investitionen in die Automatisierung, die Schaffung von Kompetenzzentren sowie den Aufbau regionaler Lieferketten umfasst. Wir setzen auf den neuesten Stand der Technik, um Kosten- und Umwelteffizienz zu steigern, die Produktqualität zu optimieren, das Kundenerlebnis zu verbessern und die Sicherheit zu erhöhen.
Digitalisierung der Werke
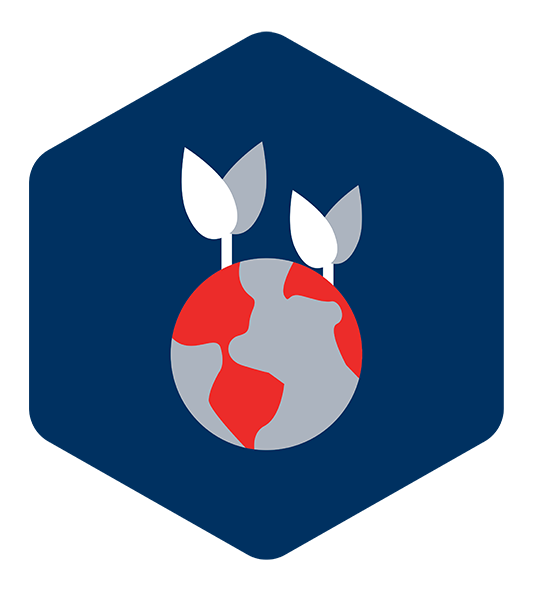
Emissionen bis 2025 reduzieren
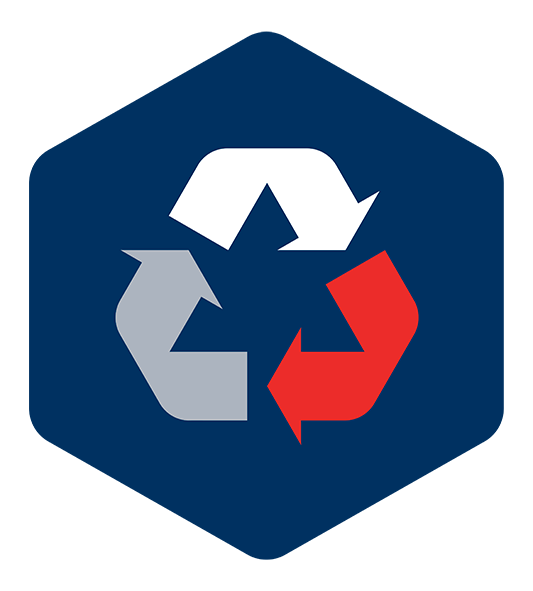
Sekundärrohstoffe in Feuerfestmaterialien
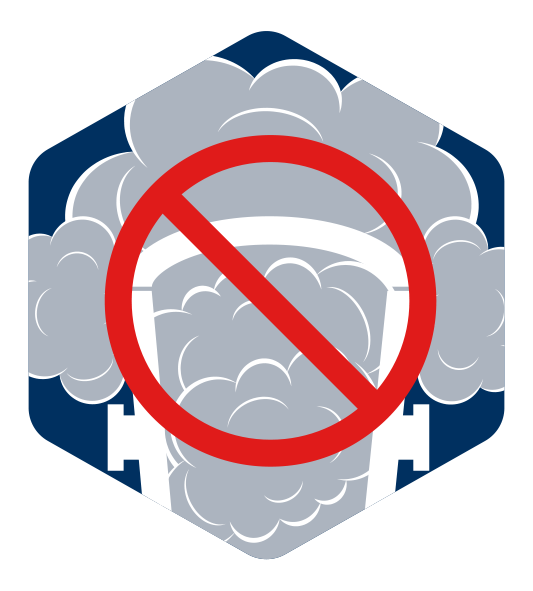
Netto-Null-Emissionen
Intelligente Produktionsprozesse: Digitalisierung unseres Netzwerks
Die Technologie, die wir unternehmensweit zur Optimierung und Integration von Produktionsprozessen nutzen, ist ein wesentliches Element unserer globalen digitalen Transformation. Dazu werden computergestützte Netzwerke, sogenannte Manufacturing Execution Systeme (MES), eingesetzt, um Prozesse vom Rohstoff bis hin zum fertigen Feuerfestprodukt in unseren Werken in Österreich und China zu verfolgen und zu dokumentieren.
MES wird …
- die Produktionsprozesse reibungsloser und schneller machen
- Daten in Echtzeit erfassen
- Effizienz und Produktqualität steigern
- Kosten senken
- und rasch auf Innovationen und Optimierungen im Produktionsbereich reagieren.
Wir wollen eine eigenständige, hoch skalierbare und Open-Source-MES-Plattform aufbauen, die in den nächsten Jahren zügig auf andere Werke ausgeweitet werden kann.
Neben zahlreichen Vorteilen wie höherer Kundenzufriedenheit, verbessertem MitarbeiterInnenengagement sowie optimierter Liquidität durch eine Reduktion des Lagerbestands in den Werken, erwarten wir auch dass die Anlageneffektivität insgesamt verbessert wird. Ebenso sparen wir bei Wartungs- und Energiekosten ein und verzeichnen eine bessere Umweltperformance.
Virtuelle Realität
Als Reisen im Jahr 2020/2021 während der Covid-19 Pandemie massiv eingeschränkt waren, gelang es RHI Magnesita mithilfe von Virtual-Reality-Lösungen (VR), Besuche bei Kunden oder Aktivitäten an eigenen Standorten erfolgreich fortzusetzen. Dazu gehörten zum BeispielSmart Glasses, die bei der Inspektion und Bewertung neuer, in China gebauter Pressen verwendet wurden: Der Einsatz von VR ermöglichte Technikexperten aus Brasilien und Europa hier eine Remote-Teilnahme am Factory Acceptance Test.
Digitale Technologien: APO und QCK
Automated Process Optimization (APO) und Quick Check (QCK) zählen zu den zentralen Maßnahmen in der digitalen Transformationsstrategie des Unternehmens.
- APO ist RHI Magnesitas einzigartige digitale Lösung, die mithilfe von künstlicher Intelligenz die Lebensdauer von Feuerfestprodukten vorhersagt. In jeder Phase des Produktionsprozesses werden Daten erfasst und für Prognosen über Leistung, erforderliche Wartungsarbeiten und die Erneuerung von Feuerfestprodukten genutzt. Im Februar 2021 wurde RHI Magnesita für die APO-Technologie als eines von sechs Unternehmen mit dem Microsoft Intelligent Manufacturing Award ausgezeichnet. Mit diesem Preis werden Industriepioniere gewürdigt, die Exzellenz durch Digitalisierung unter Beweis stellen und mit innovativen Ideen und kreativen Ansätzen den Wandel vorantreiben.
- Quick Check (QCK) ist die intelligente Messlösung unseres Unternehmens. Auf Basis einer innovativen Bildverarbeitungstechnologie wird mithilfe von 3D-Scans der Verschleiß von Auskleidungen gemessen. QCK kann Bilder zehnmal schneller als die modernste Lasertechnologie produzieren – und das bei deutlich höherer Auflö Diese qualitativ hochwertigeren Inputdaten kommen dann in der Automated Process Optimization (APO) Lösung zum Einsatz, sodass präzisere Vorhersagen erstellt werden können.
Strategische Partnerschaft für digitale Transformation
Wir sind 2020 eine strategische Partnerschaft mit Microsoft eingegangen, um unser digitales Angebot zu forcieren und in der Zusammenarbeit mit unseren KundInnen neue Wege zu gehen. Zu den Initiativen im Rahmen der Partnerschaft zählen:
- 360° Customer View
- Next Best Action (NBA) Engine
- RFID-Rückverfolgbarkeit
- Machinery Connection
- Remote Assist
- unser vernetzter Außendienst
- unsere Sales Chat Funktion
Der Weg zur Digitalisierung bringt einen umfassenden Wandel innerhalb unseres Geschäfts mit sich, der unsere Resilienz stärken wird, es uns ermöglicht, ein herausragendes Kundenerlebnis anzubieten und rasch auf die sich rasant entwickelnde digitale Zukunft zu reagieren, die vor uns liegt.
Innovation fördern
Um Innovationen zu fördern, haben wir 2020 unter anderem folgende Initiativen umgesetzt:
- Technologie-Roadmap: Durch die Zusammenarbeit in einem interdisziplinären Team wollen wir neue Technologien, Trends und Einflüsse, die sich auf die Zukunft unserer Industrie auswirken, besser verstehen.
- Innovation durch unsere “Innochallenge” forcieren: Diverse Teams untersuchen neun Ausgangsideen, die sich mit neuen Technologien und agiler Methodik befassen. Vier davon werden 2021 mit Budget- und Zeitressourcen gefö
- Offene Innovationsplattform: Gemeinsam mit unserem Partner Nine Sigma haben wir 2020 Lösungen und geeignete ExpertInnen gefunden, um an acht verschiedenen Herausforderungen – von CO2-Reduktion bis Recycling – zu arbeiten.
Innovation fördern, um Werte zu schaffen
Wir arbeiten sowohl in der Rohstoff- als auch in der Feuerfestproduktion ständig an Innovationen mit dem Ziel, Feuerfesteigenschaften und -effizienz zu verbessern, Emissionen zu reduzieren und energie- sowie kosteneffizient zu arbeiten. Ein Beispiel dafür ist die Spinosphere-Technologie, die in unserer ANKRAL-X Serie zum Einsatz kommt. Sie zeichnet sich durch einzigartige Klinkerschmelzbeständigkeit und Flexibilität bei Drehrohrofensteinen aus. Korrosionswiderstand und mechanische Festigkeit für Anwendungen in der Stahlindustrie konnten so verbessert werden. Darüber hinaus haben wir in Form unserer ANKRAL LC Serie eine kohlenstoffarme Technologie für den Einsatz in der Zementindustrie entwickelt. Diese weisen im Vergleich zu herkömmlichen Produkten einen deutlich geringeren CO2-Fußabdruck auf. Zudem soll diese Serie Abfall minimieren und den Einsatz von Recyclingmaterialien maximieren.
Unser Weg zu Netto-Null-Emissionen und Kreislaufwirtschaft
Eine unserer fünf wichtigsten Prioritäten als Unternehmen ist das Ziel von Netto-Null-Emissionen.
Wir haben unsere Kräfte gebündelt und verstärkt, um unser Ziel für 2025 zu erreichen: eine Reduktion der Scope 1, 2 und 3 (Rohstoffe) Emissionen um 15%. Da unsere Industrie besonders energieintensiv ist, stellt dies eine enorme Herausforderung dar. Wir wollen unser Ziel auf konventionelle Art und Weise erreichen: durch mehr Recycling, verbesserte Energieeffizienz, Brennstoffwechsel und die Verwendung von Ökostrom. Das größte unmittelbare Potenzial, Emissionen zu senken, hat dabei Recycling. Wir wollenden Gehalt sekundärer Rohstoffe (SRM) bis 2025 auf 10 % erhöhen und haben in jeder Region Recyclinganlagen errichtet oder errichten diese aktuell. Die Maßnahmen in Richtung einer Kreislaufwirtschaft werden auch den Prozess hin zu niedrigeren Emissionen beschleunigen.
Dennoch werden uns konventionelle Maßnahmen allein nicht zu Netto-Null-Emissionen führen. Nahezu 50 % unserer Emissionen entstehen auf natürliche Weise und werden bei der Verarbeitung von Mineralien freigesetzt. Kohlendioxid (CO2) wird emittiert, wenn Rohmagnesit (MgCO3) zu Magnesia (MgO), der Basis für zahlreiche Feuerfestprodukte, verarbeitet wird. Es braucht neue Technologien, die ermöglichen, dass das freigesetzte CO2 zuerst abgeschieden und dann für industrielle Zwecke als Rohstoff eingesetzt wird. Rund um dieses Abgas muss eine vollkommen neue Wertschöpfungskette aufgebaut werden.
Unser F&E-Bereich und unser Technischer Beirat (Technical Advisory Committee, TAC) arbeiten mit führenden Forschungseinrichtungen und Industriepartnern zusammen, um die vielversprechendsten Technologien zur Abscheidung und Nutzung dieser geogenen Emissionen zu ermitteln. In den nächsten vier bis fünf Jahren werden wir 50 Millionen Euro investieren, um diese Technologien zu testen. 2021 starten an unseren beiden österreichischen Standorten Industrieversuche, die einen wichtigen Schritt in Richtung Netto-Null darstellen: Sollten sie erfolgreich sein, werden wir bereit sein, die Technologie auszurollen, die uns an unseren Produktionsstandorten weltweit zu Netto-Null zu führen kann.